Potential Supply Chain Risks and Mitigation Approaches
- Abuzar Talibov
- Sep 13, 2022
- 2 min read
Updated: Oct 29, 2023
Hundreds of Millions of US Dollars (!) - these are the recall costs arising every year from the variety of disruptions in Supply-Chain of the main industries such as pharmaceuticals, consumer goods, electronics and automotive.

In general, potential risks refer to uncertainties and disruptions that can affect the flow of goods and services from suppliers to end customers. These can arise from different types of factors, including natural disasters, geopolitical instability, economic shifts, cyberattacks, supplier bankruptcies, and quality issues.
Although companies are constantly working on the mitigation of risks in Supply-Chain, the recent global complexities like the jam in the Suez Canal in Egypt or the COVID-19 pandemic, forced them to implement proper adaption measures.
Figure 1: Suez canal Blockade
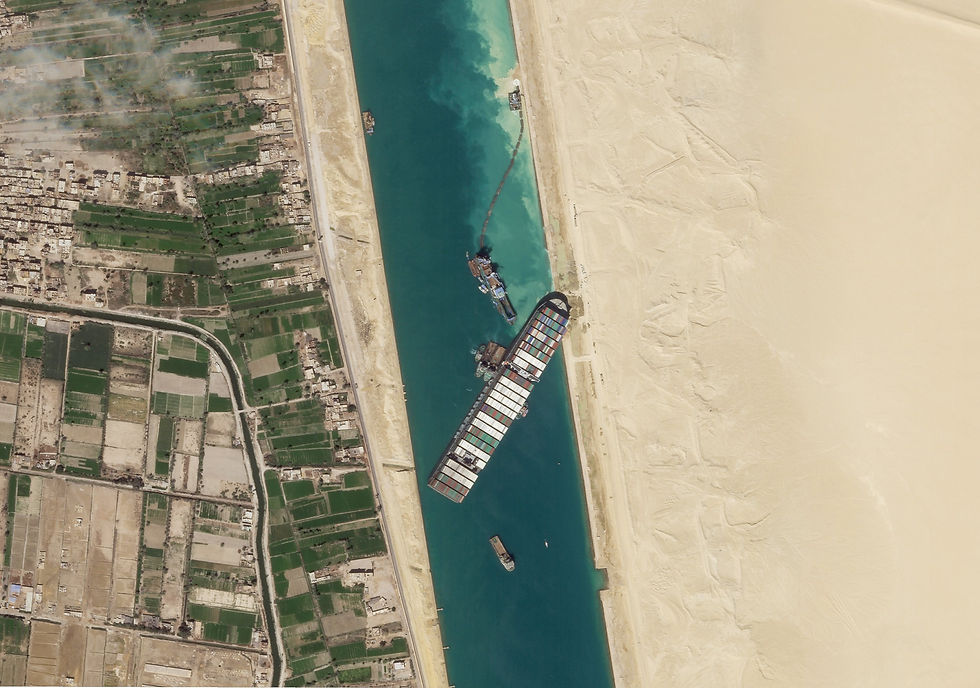
Since the Supply-Chain has been globalised in more or less all industries, the recent COVID-19 pandemic, which resulted in factory closures, transportation disruptions, and increased demand for certain products, such as personal protective equipment (PPE) and medical supplies, diffused into all sectors of the global economy.
Based on the survey that has been conducted by EY, 72% of participating companies verified the negative influence of COVID-19 on their businesses. However, those companies that have been investing in their technological adaptation, could decrease those effects.
Figure 2: Effects of COVID-19 on Companies

It's important to mention that the more economy becomes global and the more technological solutions companies implement, the more complications we see in the Supply-Chain. Therefore, apart from pandemic-related difficulties, the issues like Cybersecurity, geopolitical risks, and labour shortages are becoming a high priority.
Basically, effective Supply-Chain risk management involves identifying and assessing potential risks in the first place, then developing contingency plans, and building resilience into the supply chain to mitigate the effects of disruptions.
Based on market research, there are several strategies that organisations can use to mitigate supply chain risks. These include:
Diversifying suppliers and geographies
By working with multiple suppliers and geographies, organisations can reduce their reliance on a single supplier or location and minimise the impact of disruptions.
Building inventory buffers
Maintaining inventory buffers can help organisations manage unexpected supply chain disruptions and avoid stockouts. Of course, this should be optimized to avoid further inventory costs
Developing contingency plans
Organisations can develop contingency plans (so-called "Plan "B") that outline specific actions to take in response to potential risks
Strengthening supplier relationships
Building strong relationships with suppliers can improve communication and collaboration and help address potential risks, like Efficient Consumer Response (ECR)
Investing in technology
The use of technology, such as real-time monitoring/tracking and predictive analytics, can help organisations detect and respond to potential supply chain risks more quickly and effectively
Conducting regular risk assessments
Regularly assessing potential supply chain risks can help organisations identify new risks and ensure that risk management strategies remain up-to-date and effective
Overall, a comprehensive risk management approach involves a combination of these strategies and continuous monitoring to ensure the Supply-Chain remains resilient to potential risks. Companies can adapt and customize the approaches according to their business strategy.
Of course, there will be uncontrollable situations emerging from unknown risks. For those cases, McKinsey provides a quite useful defence method for the companies.
Figure 3: Layers of Defences Help Organisations Manage Unknown Risks

Sources